What is a Thermocouple Sensor?
According to the thermal electromotive force as a function of temperature, a thermocouple indexing table is prepared; The index table is obtained under the condition that the free end temperature is 0 ° C, and different thermocouples have different index tables.
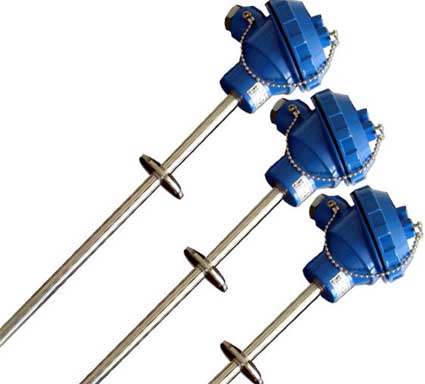
What is the application of the thermocouple sensor?
A thermocouple is formed by joining two different conductors together. The so-called thermal electromagnetic force (EMF) is produced when the measurement and reference junctions are at different temperatures, respectively. Connection Point Use The measurement connection point is the portion of the thermocouple connection point at the temperature being measured. The reference junction is the portion of the thermocouple junction that remains at a known temperature or that is automatically compensated for by temperature changes.
In conventional industrial applications, thermocouple elements are typically terminated on a joint; However, the reference junction is rarely located on the connector, but is instead routed to a temperature-stable controlled environment using an appropriate thermocouple extension line. The connection point type shell-type thermocouple junction is physically connected (welded) to the probe wall, which enables good heat transfer—that is, heat is transferred from the outside through the probe wall to the thermocouple junction. Shelled thermocouples are recommended for measuring the temperature of static or flowing corrosive gases and liquids, as well as some high pressure applications. In an insulated thermocouple, the thermocouple junction is separated from the probe wall and surrounded by a soft powder. Although an insulated thermocouple responds more slowly than a shell-type thermocouple, it provides electrical insulation. Insulated thermocouples are recommended for measuring corrosive environments and are ideally insulated from the surrounding environment by a jacket shield. Open-ended thermocouples allow the tip of the joint to penetrate deep into the surrounding environment. This type provides optimum response time, but is limited to use in non-corrosive, non-hazardous and non-pressurized applications. The response time is expressed as a time constant defined as the time required for the sensor to change 63.2% between the initial and final values in the controlled environment. Open-ended thermocouples have the fastest response speed, and the smaller the probe sheath diameter, the faster the response, but the lower the maximum allowable measurement temperature. The extension line thermocouple extension line is a pair of wires having the same temperature electromagnetic frequency characteristics as the thermocouples connected thereto. When the connection is appropriate, the extension line will be transferred from the thermocouple to the other end of the line with reference to the connection point, which is usually located in the controlled environment.
1. The temperature range to be measured;
2, the required response time;
3. Connection point type;
4. Chemical resistance of thermocouple or sheath material;
5, anti-wear or anti-vibration ability;
6, installation and restrictions, etc.