Use NTC component temperature sensing to protect fast charging devices
Portable electronics are growing rapidly. From cell phones and MP3 players to PDAs, personal DVD players and more traditional laptops. People began to revisit many aspects of consumer and professional product design.
This change is most evident in battery technology. Users want batteries to meet increasingly complex application needs, so they need more current and longer working hours. At the same time, the demand for small, lightweight products is also very strong, and the battery accounts for a considerable proportion of the volume and weight of any device. Therefore, manufacturers pay great attention to reducing their size and weight. Another point is the requirement for fast charging, that is, reducing the time that the user waits for charging, and maximizing the advantages of mobility.
These requirements have prompted battery manufacturers to switch to new chemical materials such as nickel-metal hydride and lithium-ion to achieve higher power density, lighter weight and faster charging speeds. These features, especially fast charging, come at the cost of increased complexity. New batteries require precisely controlled charging circuits that not only ensure that they are fully charged, but also maximize their useful life and prevent possible hazards from overheating.
Failure of any component of the battery pack can have very serious consequences, not just because the product itself cannot be used because it cannot be powered. Recently, a company has recalled a number of laptop-specific batteries, which are estimated to cause losses of up to $400 million. In addition to possible financial damage, the battery can cause personal injury and even cause a fire.
Design effective control strategies for battery charging (especially for high-energy lithium-ion batteries). Good design and proper component specifications and procurement policies are required. The following architectures are available: For NiMH batteries, the charge control loop can monitor (using various levels of accuracy) the battery voltage as a function of time. It is also possible to limit the maximum charging time; Or let the system monitor for temperature changes. In most cases, some kind of temperature monitoring method is needed to provide protection.
Lithium-ion batteries typically use a CCCV (constant current-constant voltage) scheme. However, this still requires monitoring the temperature to allow for fast charging to be initiated, while also requiring a mechanism to ensure that charging is stopped when the temperature exceeds a safe threshold.
Therefore, all of these control and protection strategies should include temperature monitoring mechanisms as an integral part of the overall functional system. ICs that are typically placed in a charger or battery provide monitoring and control functions. But be sure to install one or more temperature sensors in the battery, charger, or battery compartment (as is often the case with low-cost phones).
For designers, the choice of such sensors is not large. Thermocouple devices require relatively complex compensation circuits, which can cause some calibration problems. In addition, they produce output voltages of a few mV, require signal conditioning, and are susceptible to electromagnetic noise.
Nickel or platinum positive temperature coefficient (PTC) metal film (or wire wound) resistors are sometimes used. Their long-term stability is better than thermocouple devices and is less susceptible to noise. However, since they rely on current flowing through themselves to monitor temperature, and are typically low impedance devices, the power consumption is relatively high. And they are not sensitive enough to temperature changes to achieve reliable temperature monitoring. Most linear PTC semiconductor devices on the market have this drawback.
At present, the most effective solution is to use NTC (negative temperature coefficient) thermistor under the premise of reasonable cost performance. The NTC class from Yaxun Electronics is a compact solution that consumes very little power, has excellent accuracy over a wide temperature range, and reacts quickly to temperature changes. From the engineer's point of view, these specifications of the devices provide a very high degree of flexibility for the electrical and structural design.
The most basic design and specification parameters for NTC devices are resistance values (usually values at 25 ° C) and tolerances. However, it must be remembered that the thermistor works closely with temperature. Therefore, engineers must ensure that their products are designed to work properly when the operating temperature reaches the limit. In high temperature (low impedance) environments, the value of the resistor must be high enough to reduce system errors such as contact resistance and interconnect resistance. Conversely, in a low temperature (high impedance) environment, if the current through the thermistor is not large enough, the sensitivity will decrease.
Tolerances are usually expressed in °C and can be used as a measure of the accuracy of the device's measurement of temperature. In a few cases, the manufacturer will give a tolerance expressed in terms of resistance value, ie how close the device resistance is to its expected resistance value at a given temperature. For detailed specifiers and buyers, it is important to keep in mind the following points. That is, the tolerance requirements for a particular design can be limited to a specific temperature or to a slightly wider temperature range. In the second case, the tolerance itself vary with the absolute value of the resistance of the device. Designers need to calculate the resistance tolerance over the entire temperature range using the negative temperature coefficient specified for the device to ensure that the selected component meets the measurement accuracy requirements of the system.
The performance of the device is dependent on its material and structure over the operating temperature range and is described by the third basic specification, the device's R-T curve.
When using NTC-based devices, designers often specify only resistors, tolerances, and standard curves. However, in many cases other parameters are the key to ensuring that the system works as expected.
One of the most important parameters is the value of B, which indicates the sensitivity of the resistance of the device to temperature. Equally important is the calibration tolerance of the parameter. Yaxun electronics devices have excellent B-values and tolerances for higher accuracy and better overall system reliability. It also has good performance over the entire operating temperature range of the device.
Finally, what is often overlooked by the buyer is that NTC-type devices need to be tightly mounted at the required temperature test points. This means that the component must be able to withstand the physical stresses of modern manufacturing processes. Especially in the case of a steep temperature profile in a RoHS-compliant lead-free process.
This change is most evident in battery technology. Users want batteries to meet increasingly complex application needs, so they need more current and longer working hours. At the same time, the demand for small, lightweight products is also very strong, and the battery accounts for a considerable proportion of the volume and weight of any device. Therefore, manufacturers pay great attention to reducing their size and weight. Another point is the requirement for fast charging, that is, reducing the time that the user waits for charging, and maximizing the advantages of mobility.
These requirements have prompted battery manufacturers to switch to new chemical materials such as nickel-metal hydride and lithium-ion to achieve higher power density, lighter weight and faster charging speeds. These features, especially fast charging, come at the cost of increased complexity. New batteries require precisely controlled charging circuits that not only ensure that they are fully charged, but also maximize their useful life and prevent possible hazards from overheating.
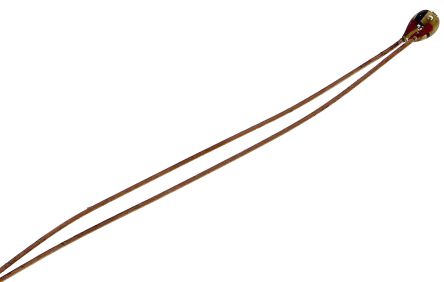
Failure of any component of the battery pack can have very serious consequences, not just because the product itself cannot be used because it cannot be powered. Recently, a company has recalled a number of laptop-specific batteries, which are estimated to cause losses of up to $400 million. In addition to possible financial damage, the battery can cause personal injury and even cause a fire.
Design effective control strategies for battery charging (especially for high-energy lithium-ion batteries). Good design and proper component specifications and procurement policies are required. The following architectures are available: For NiMH batteries, the charge control loop can monitor (using various levels of accuracy) the battery voltage as a function of time. It is also possible to limit the maximum charging time; Or let the system monitor for temperature changes. In most cases, some kind of temperature monitoring method is needed to provide protection.
Lithium-ion batteries typically use a CCCV (constant current-constant voltage) scheme. However, this still requires monitoring the temperature to allow for fast charging to be initiated, while also requiring a mechanism to ensure that charging is stopped when the temperature exceeds a safe threshold.
Therefore, all of these control and protection strategies should include temperature monitoring mechanisms as an integral part of the overall functional system. ICs that are typically placed in a charger or battery provide monitoring and control functions. But be sure to install one or more temperature sensors in the battery, charger, or battery compartment (as is often the case with low-cost phones).
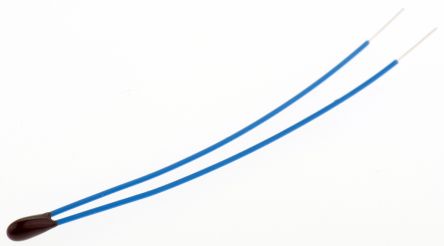
For designers, the choice of such sensors is not large. Thermocouple devices require relatively complex compensation circuits, which can cause some calibration problems. In addition, they produce output voltages of a few mV, require signal conditioning, and are susceptible to electromagnetic noise.
Nickel or platinum positive temperature coefficient (PTC) metal film (or wire wound) resistors are sometimes used. Their long-term stability is better than thermocouple devices and is less susceptible to noise. However, since they rely on current flowing through themselves to monitor temperature, and are typically low impedance devices, the power consumption is relatively high. And they are not sensitive enough to temperature changes to achieve reliable temperature monitoring. Most linear PTC semiconductor devices on the market have this drawback.
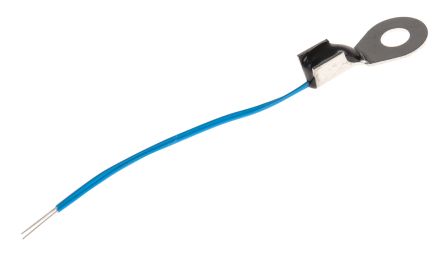
The most basic design and specification parameters for NTC devices are resistance values (usually values at 25 ° C) and tolerances. However, it must be remembered that the thermistor works closely with temperature. Therefore, engineers must ensure that their products are designed to work properly when the operating temperature reaches the limit. In high temperature (low impedance) environments, the value of the resistor must be high enough to reduce system errors such as contact resistance and interconnect resistance. Conversely, in a low temperature (high impedance) environment, if the current through the thermistor is not large enough, the sensitivity will decrease.
Tolerances are usually expressed in °C and can be used as a measure of the accuracy of the device's measurement of temperature. In a few cases, the manufacturer will give a tolerance expressed in terms of resistance value, ie how close the device resistance is to its expected resistance value at a given temperature. For detailed specifiers and buyers, it is important to keep in mind the following points. That is, the tolerance requirements for a particular design can be limited to a specific temperature or to a slightly wider temperature range. In the second case, the tolerance itself vary with the absolute value of the resistance of the device. Designers need to calculate the resistance tolerance over the entire temperature range using the negative temperature coefficient specified for the device to ensure that the selected component meets the measurement accuracy requirements of the system.
The performance of the device is dependent on its material and structure over the operating temperature range and is described by the third basic specification, the device's R-T curve.
When using NTC-based devices, designers often specify only resistors, tolerances, and standard curves. However, in many cases other parameters are the key to ensuring that the system works as expected.
One of the most important parameters is the value of B, which indicates the sensitivity of the resistance of the device to temperature. Equally important is the calibration tolerance of the parameter. Yaxun electronics devices have excellent B-values and tolerances for higher accuracy and better overall system reliability. It also has good performance over the entire operating temperature range of the device.
Finally, what is often overlooked by the buyer is that NTC-type devices need to be tightly mounted at the required temperature test points. This means that the component must be able to withstand the physical stresses of modern manufacturing processes. Especially in the case of a steep temperature profile in a RoHS-compliant lead-free process.
PREVIOUS:NONE
NEXT:NTC temperature control circuit diagram of a sensor used in refrigerators
NEXT:NTC temperature control circuit diagram of a sensor used in refrigerators