The working principle and application of linear ntc temperature sensor
The linear temperature sensor is a linearized output negative temperature coefficient (ntc) thermal element. It is actually a linear temperature-voltage conversion component, that is to say, under the condition of operating current (100ua), the component voltage value changes linearly with temperature, achieving a linear conversion from non-electricity to electricity. The main feature of the linear ntc temperature sensor is the temperature-voltage relationship in the operating temperature range. The secondary development of temperature measurement and temperature control circuit design will complete the temperature measurement or temperature control circuit design without simplifying the linearization process, simplifying the design and debugging of the instrument. The principle of extension line selection should be followed:
Generally -200 ~ +20 ° C, -50 ~ +100 ° C should choose ordinary double glue line; 100 ~ 200 ° C range should use high temperature line.
The meaning of the reference voltage:
The reference voltage refers to the voltage value on the sensor when the sensor is placed in the 0°C temperature field (ice water mixture) and the operating current (100μa). In fact, it is the 0 point voltage. The symbol is v(0), the value is calibrated at the factory, and the temperature coefficient s of the sensor is the same. If the reference voltage value v(0) is known, the sensor voltage value at any temperature point can be known without dividing the sensor. Its calculation formula is:
v(t)=v(0)+s×t
Example: such as reference voltage v (0) = 700mv; The temperature coefficient s = -2 mv / ° C, then at 50 ° C, the sensor output voltage v (50) = 700 - 2 × 50 = 600 (mv). This is where linear temperature sensors are superior to other temperature sensors.
The linear ntc temperature sensor temperature range specifies:
In general, the temperature range can be between -200 and +200 °C. However, considering the actual needs, it is generally unnecessary to have such a wide temperature range, and three different sections are specified to suit different package designs, and the extension line selection is also different. For temperature-compensated linear thermal sensors, the operating temperature range is only -40°C to +80°C. Can fully meet the general circuit temperature compensation.
The meaning of the temperature coefficient s:
The temperature coefficient s refers to the ratio of the change of the output voltage value of the sensor to the temperature change under the specified working conditions, that is, the value of the sensor output voltage change every 1 °C change in temperature: s = Δv / Δt (mv / ° C).
The temperature coefficient is the linear temperature sensor as the physical basis of the temperature measuring component, and its function is similar to the thermistor b value. This parameter has the same value over the entire operating temperature range, ie -2mv/°C, and the sensors of the various models are also the same value. This traditional thermistor temperature sensor is unparalleled.
The meaning of this parameter of interchangeability:
Interchange accuracy refers to the same determined ideal fit line under the same working conditions (same working current, same temperature field). The maximum deviation of each sensor voltage v(t)-temperature t curve from the line is usually expressed by the temperature-voltage conversion coefficient s of the sensor. The sensor output is linearized and the temperature-voltage conversion factor is the same, that is, the entire range is interchanged within the temperature range. The interchange accuracy indicates the degree of dispersion of the reference voltage value, that is, the discrete value of the reference voltage value is converted into a temperature value to describe the degree of interchange between the entire batch of sensors.
Generally divided into three levels:
i-level interchange deviation is less than 0.3 deg.] C;
j level is not more than 0.5 ° C;
The k level is not more than 1.0 °C.
The meaning of linearity:
Linearity is a measure of the linearity of the sensor output voltage value as a function of temperature. In fact, it is the maximum deviation of the ideal fit straight line in the operating temperature range of the sensor output voltage. In general, the linearity is typically ±0.5%. Obviously, the higher the linearity of the sensor (the smaller the value), the simpler the instrument design, and the instrument input stage does not have to be linearized.
Linear temperature sensors are the reason for normalizing the output:
The so-called normalized output is the operating condition under the sensor at 0 ° C temperature point. The output voltage value is limited to a small range, not interchangeable, and its reference voltage value is only limited between 690-710mv. When designing the circuit in this way, it is easy to grasp the sensor output situation macroscopically, and the bridge design temperature compensation, considering between 690-710mv, a little adjustment can be made during debugging. Unlike ordinary thermistor models, the resistance values are the same. For different models, different design calculations are required. The linear temperature sensor normalizes the output, enabling the instrument circuit to be standardized.
Whether the actual temperature sensor must be analyzed by constant current source power supply:
In general, it is unnecessary, and the bridge voltage constant voltage supply is complete (see 16 sensor signal processing circuits). This is a sensor current temperature-voltage conversion coefficient with a small amount of current around 100μa, which can give a measured magnitude concept:
When 100μa s=-2mv/°C
At 40μa s=-2.1mv/°C
s=-1.9mv/°C at 1000μa
When the actual bridge is supplied with constant voltage, the current change will not be so large.
When the constant voltage is supplied, the sensor load resistance value is determined as follows:
During constant voltage supply, the load resistor is connected between the power supply and the positive terminal of the sensor, and the signal is output from between the positive and negative terminals of the sensor. When designing the resistance value r, the sensor operating current is 100 μa at 0c. If the sensor reference voltage is v(0)(mv) and the constant voltage source is vdd(mv), then r=(vdd-v(0))(mv)/0.1(ma). Calculate the resistance value r, the actual resistance does not have such resistance value, can be selected near the resistance value, has no effect on the temperature measurement accuracy.
Linear temperature compensation components are used as circuit temperature compensation advantages:
This mainly considers the standardization of the output of the thermal element and the consistency of the temperature coefficient, which is convenient for design. In addition, the temperature coefficient is the same as the transistor base and emitter voltage temperature coefficients in the transistor circuit, and it is very suitable as a base biasing element for stabilizing the transistor circuit operating point. When several components are used in series, the potentiometer can be connected in parallel, and the potentiometer can adjust different temperature coefficients to achieve accurate temperature compensation (see Figure 3). This temperature coefficient adjustable compensating component does not require complicated design and does not have strict requirements on the operating current of the component. This is also a great advantage of this linear thermal element for temperature compensation.
Differences between civilian and industrial use:
The main interchange accuracy is different. A single instrument for high-volume group measurement applications, and the test accuracy requires a higher industrial environment, it is recommended to use industrial grade; And one meter uses only one sensor, and the bulk reliability is very high. It is recommended to use civilian grade.
Sensor signal processing circuit:
Note: The bridge is r2 to cancel the sensor reference voltage value v(0), that is, the voltage on the adjustment r2 is equal to the sensor reference voltage value. This causes the bridge to output 0c as 0v, and then outputs -2mv/c to the amplifier or the next stage circuit. As the temperature control circuit design, the voltage on r2 is output to the non-inverting terminal of the comparator, the sensor output is connected to the inverting terminal of the comparator, and r2 is selected according to the temperature of the control temperature.
The formula can be used to calculate v(t)=v(0)+s×t to, where v(0) is the sensor reference voltage value (given at the factory), s is the temperature coefficient of the sensor voltage (given at the factory), t is the temperature control point temperature value. It is recommended that r2 use a multi-turn potentiometer to set the temperature control point more accurately.
Whether linear ntc temperature sensors can replace thermistors, thermocouples, and other RTDs:
-200 ~ +200c temperature range can be completely replaced, no major changes to the original circuit, no linearization of the sensor. The two parameters of the reference voltage value and the voltage temperature coefficient can be used to design the circuit. These two parameters are calibrated by the manufacturer at the factory, and the parameters are unchanged for the same user and different batches of products.
The meaning of stability:
Stability refers to the annual drift of the sensor's reference voltage value. This drift is then converted into a temperature value according to the temperature-voltage conversion coefficient, ie, stability = ± Δv / s / year. Linear temperature sensor stability is ±0.05 °C / year. This parameter describes the ability of the sensor to maintain its original characteristics under various conditions of use.
Analysis of whether long-line transmission affects the sensor signal:
It should be said that the impact is not large, under normal circumstances, the transmission distance can reach more than 1000 meters. Farther away, you can consider converting the sensor output signal into a digital quantity, which makes it easier to transmit over long distances.
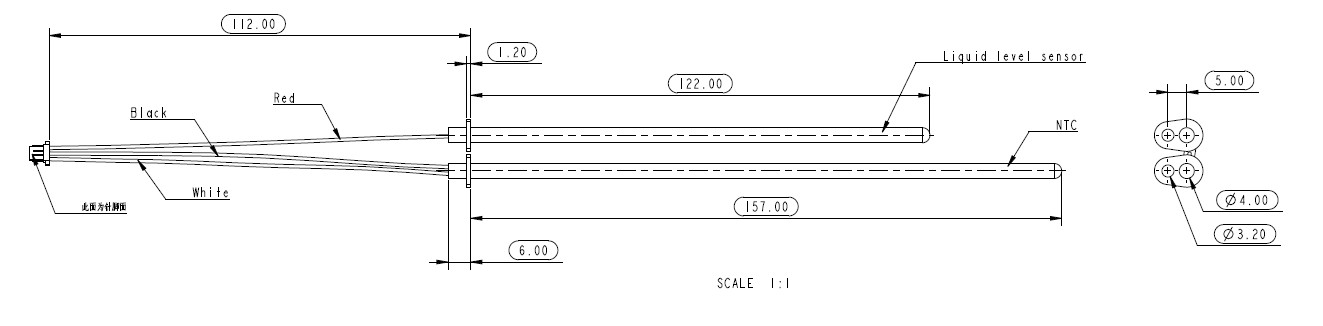
Generally -200 ~ +20 ° C, -50 ~ +100 ° C should choose ordinary double glue line; 100 ~ 200 ° C range should use high temperature line.
The meaning of the reference voltage:
The reference voltage refers to the voltage value on the sensor when the sensor is placed in the 0°C temperature field (ice water mixture) and the operating current (100μa). In fact, it is the 0 point voltage. The symbol is v(0), the value is calibrated at the factory, and the temperature coefficient s of the sensor is the same. If the reference voltage value v(0) is known, the sensor voltage value at any temperature point can be known without dividing the sensor. Its calculation formula is:
v(t)=v(0)+s×t
Example: such as reference voltage v (0) = 700mv; The temperature coefficient s = -2 mv / ° C, then at 50 ° C, the sensor output voltage v (50) = 700 - 2 × 50 = 600 (mv). This is where linear temperature sensors are superior to other temperature sensors.
The linear ntc temperature sensor temperature range specifies:
In general, the temperature range can be between -200 and +200 °C. However, considering the actual needs, it is generally unnecessary to have such a wide temperature range, and three different sections are specified to suit different package designs, and the extension line selection is also different. For temperature-compensated linear thermal sensors, the operating temperature range is only -40°C to +80°C. Can fully meet the general circuit temperature compensation.
The meaning of the temperature coefficient s:
The temperature coefficient s refers to the ratio of the change of the output voltage value of the sensor to the temperature change under the specified working conditions, that is, the value of the sensor output voltage change every 1 °C change in temperature: s = Δv / Δt (mv / ° C).
The temperature coefficient is the linear temperature sensor as the physical basis of the temperature measuring component, and its function is similar to the thermistor b value. This parameter has the same value over the entire operating temperature range, ie -2mv/°C, and the sensors of the various models are also the same value. This traditional thermistor temperature sensor is unparalleled.
The meaning of this parameter of interchangeability:
Interchange accuracy refers to the same determined ideal fit line under the same working conditions (same working current, same temperature field). The maximum deviation of each sensor voltage v(t)-temperature t curve from the line is usually expressed by the temperature-voltage conversion coefficient s of the sensor. The sensor output is linearized and the temperature-voltage conversion factor is the same, that is, the entire range is interchanged within the temperature range. The interchange accuracy indicates the degree of dispersion of the reference voltage value, that is, the discrete value of the reference voltage value is converted into a temperature value to describe the degree of interchange between the entire batch of sensors.
Generally divided into three levels:
i-level interchange deviation is less than 0.3 deg.] C;
j level is not more than 0.5 ° C;
The k level is not more than 1.0 °C.
The meaning of linearity:
Linearity is a measure of the linearity of the sensor output voltage value as a function of temperature. In fact, it is the maximum deviation of the ideal fit straight line in the operating temperature range of the sensor output voltage. In general, the linearity is typically ±0.5%. Obviously, the higher the linearity of the sensor (the smaller the value), the simpler the instrument design, and the instrument input stage does not have to be linearized.
Linear temperature sensors are the reason for normalizing the output:
The so-called normalized output is the operating condition under the sensor at 0 ° C temperature point. The output voltage value is limited to a small range, not interchangeable, and its reference voltage value is only limited between 690-710mv. When designing the circuit in this way, it is easy to grasp the sensor output situation macroscopically, and the bridge design temperature compensation, considering between 690-710mv, a little adjustment can be made during debugging. Unlike ordinary thermistor models, the resistance values are the same. For different models, different design calculations are required. The linear temperature sensor normalizes the output, enabling the instrument circuit to be standardized.
Whether the actual temperature sensor must be analyzed by constant current source power supply:
In general, it is unnecessary, and the bridge voltage constant voltage supply is complete (see 16 sensor signal processing circuits). This is a sensor current temperature-voltage conversion coefficient with a small amount of current around 100μa, which can give a measured magnitude concept:
When 100μa s=-2mv/°C
At 40μa s=-2.1mv/°C
s=-1.9mv/°C at 1000μa
When the actual bridge is supplied with constant voltage, the current change will not be so large.
When the constant voltage is supplied, the sensor load resistance value is determined as follows:
During constant voltage supply, the load resistor is connected between the power supply and the positive terminal of the sensor, and the signal is output from between the positive and negative terminals of the sensor. When designing the resistance value r, the sensor operating current is 100 μa at 0c. If the sensor reference voltage is v(0)(mv) and the constant voltage source is vdd(mv), then r=(vdd-v(0))(mv)/0.1(ma). Calculate the resistance value r, the actual resistance does not have such resistance value, can be selected near the resistance value, has no effect on the temperature measurement accuracy.
Linear temperature compensation components are used as circuit temperature compensation advantages:
This mainly considers the standardization of the output of the thermal element and the consistency of the temperature coefficient, which is convenient for design. In addition, the temperature coefficient is the same as the transistor base and emitter voltage temperature coefficients in the transistor circuit, and it is very suitable as a base biasing element for stabilizing the transistor circuit operating point. When several components are used in series, the potentiometer can be connected in parallel, and the potentiometer can adjust different temperature coefficients to achieve accurate temperature compensation (see Figure 3). This temperature coefficient adjustable compensating component does not require complicated design and does not have strict requirements on the operating current of the component. This is also a great advantage of this linear thermal element for temperature compensation.
Differences between civilian and industrial use:
The main interchange accuracy is different. A single instrument for high-volume group measurement applications, and the test accuracy requires a higher industrial environment, it is recommended to use industrial grade; And one meter uses only one sensor, and the bulk reliability is very high. It is recommended to use civilian grade.
Sensor signal processing circuit:
Note: The bridge is r2 to cancel the sensor reference voltage value v(0), that is, the voltage on the adjustment r2 is equal to the sensor reference voltage value. This causes the bridge to output 0c as 0v, and then outputs -2mv/c to the amplifier or the next stage circuit. As the temperature control circuit design, the voltage on r2 is output to the non-inverting terminal of the comparator, the sensor output is connected to the inverting terminal of the comparator, and r2 is selected according to the temperature of the control temperature.
The formula can be used to calculate v(t)=v(0)+s×t to, where v(0) is the sensor reference voltage value (given at the factory), s is the temperature coefficient of the sensor voltage (given at the factory), t is the temperature control point temperature value. It is recommended that r2 use a multi-turn potentiometer to set the temperature control point more accurately.
Whether linear ntc temperature sensors can replace thermistors, thermocouples, and other RTDs:
-200 ~ +200c temperature range can be completely replaced, no major changes to the original circuit, no linearization of the sensor. The two parameters of the reference voltage value and the voltage temperature coefficient can be used to design the circuit. These two parameters are calibrated by the manufacturer at the factory, and the parameters are unchanged for the same user and different batches of products.
The meaning of stability:
Stability refers to the annual drift of the sensor's reference voltage value. This drift is then converted into a temperature value according to the temperature-voltage conversion coefficient, ie, stability = ± Δv / s / year. Linear temperature sensor stability is ±0.05 °C / year. This parameter describes the ability of the sensor to maintain its original characteristics under various conditions of use.
Analysis of whether long-line transmission affects the sensor signal:
It should be said that the impact is not large, under normal circumstances, the transmission distance can reach more than 1000 meters. Farther away, you can consider converting the sensor output signal into a digital quantity, which makes it easier to transmit over long distances.
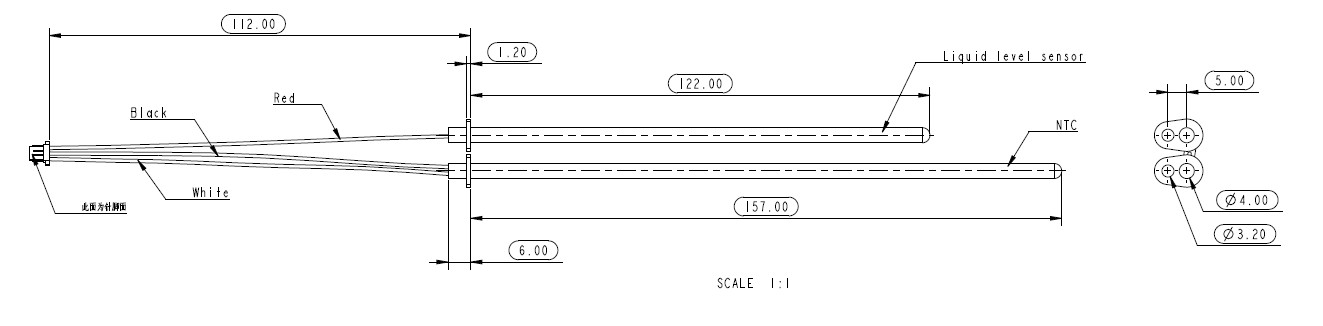