Temperature sensor time constant and hysteresis improvement measures
Transducer, The use of various physical properties of the material as a function of temperature changes the temperature into an available output signal. The temperature sensor is the core part of the temperature measuring instrument and has a wide variety. According to the measurement method, it can be divided into two types: contact type and non-contact type. According to the characteristics of sensor materials and electronic components, it is divided into two types: thermal resistance and thermocouple. The modern temperature sensor is very small in shape, which makes it widely used in various fields of production practice, and also provides countless conveniences and functions for our lives.
Temperature sensor time constant and hysteresis improvement measures
The temperature sensor time constant and hysteresis are related to the thermal capacity and thermal resistance of the temperature sensor, except for the temperature sensor with a time constant and low hysteresis. It should also ensure reasonable insertion depth and proper installation methods to ensure temperature measurement accuracy, temperature control system stability and control quality.
Temperature sensor time constant and hysteresis
Practice has proved that the thermocouple, thermistor, and the bimetal thermometer will delay the output for a period of time when the measured temperature suddenly changes. This delay time Δτ is generally called pure hysteresis or pure delay. After the delay Δτ, it will change in a law similar to the exponential curve (as shown in the figure below). If Δτ is ignored and the timing start is made with the change of the medium temperature, the above curve conforms to T=△T(1-e-t/τ), where T is the temperature; ΔT is the temperature change; t is time; τ is the time constant. The time constant corresponds to the time corresponding to the tangent of the starting point of the reaction curve and the equilibrium temperature intersection A, that is, the time required for the output to change by 63.2% ΔT.
Correct understanding and treatment of the time constant and hysteresis of temperature sensors is an important issue. It is related to whether the temperature can be measured correctly and the change of the measured temperature is reflected in time. It has a pivotal effect on the stability and quality of the temperature control system, so it is a problem that cannot be ignored. How to improve the time constant and hysteresis of the temperature sensor
How to improve the time constant and lag of temperature sensor
The temperature sensor time constant and the magnitude of the hysteresis depend on the thermal capacity and thermal resistance of the component. Because the temperature sensor needs to absorb a certain amount of heat, the heat required to change 1 °C is the heat capacity of the temperature sensor, and the smaller the heat capacity, the better. The temperature sensor heat transfer needs to overcome the thermal resistance, which is directly related to the structure and size of the component. Metal is a good conductor of heat, and the size of the thermal resistance is often affected by the air gap of the temperature sensor, the insulation, and the protective sleeve.
Temperature sensors have large time constants and hysteresis, usually ranging from tens of seconds to minutes. Therefore, the influence on the measurement and control temperature is very large, especially the stability of the temperature control system. Therefore, in the field application, in addition to the temperature sensor with a small time constant and hysteresis, it should also pay attention to the installation method of the temperature sensor. That is to say, there must be a certain insertion depth when installing, especially the thermal resistance. If the insertion depth is not enough, it will cause a large error; When the process pipe is thinner, it is necessary to locally thicken the pipe, or try to install the temperature sensor on the elbow of the pipe, so that the temperature sensor is facing the flow direction of the fluid; When measuring the temperature of the gas-liquid medium, it is preferable to measure the liquidus temperature because the dynamic characteristics and stability of the liquidus temperature are superior to the gas phase temperature; If necessary, it is also possible to fill metal foil or other heat-conducting material between the protective tube and the thermal element (the armored thermocouple or armored platinum resistor is filled with high-purity alumina powder between the protective tube and the component). For the thermocouple, an open-ended or shell-type thermocouple can also be used.
Temperature sensor time constant and hysteresis improvement measures
The temperature sensor time constant and hysteresis are related to the thermal capacity and thermal resistance of the temperature sensor, except for the temperature sensor with a time constant and low hysteresis. It should also ensure reasonable insertion depth and proper installation methods to ensure temperature measurement accuracy, temperature control system stability and control quality.
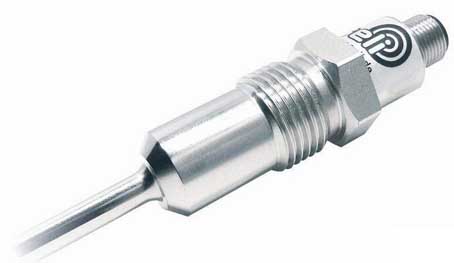
Temperature sensor time constant and hysteresis
Practice has proved that the thermocouple, thermistor, and the bimetal thermometer will delay the output for a period of time when the measured temperature suddenly changes. This delay time Δτ is generally called pure hysteresis or pure delay. After the delay Δτ, it will change in a law similar to the exponential curve (as shown in the figure below). If Δτ is ignored and the timing start is made with the change of the medium temperature, the above curve conforms to T=△T(1-e-t/τ), where T is the temperature; ΔT is the temperature change; t is time; τ is the time constant. The time constant corresponds to the time corresponding to the tangent of the starting point of the reaction curve and the equilibrium temperature intersection A, that is, the time required for the output to change by 63.2% ΔT.
Correct understanding and treatment of the time constant and hysteresis of temperature sensors is an important issue. It is related to whether the temperature can be measured correctly and the change of the measured temperature is reflected in time. It has a pivotal effect on the stability and quality of the temperature control system, so it is a problem that cannot be ignored. How to improve the time constant and hysteresis of the temperature sensor
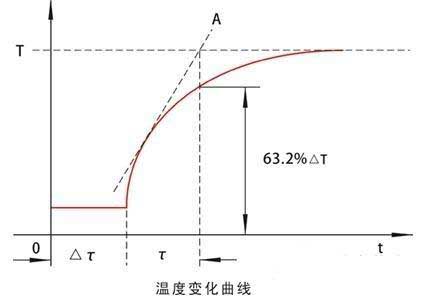
The temperature sensor time constant and the magnitude of the hysteresis depend on the thermal capacity and thermal resistance of the component. Because the temperature sensor needs to absorb a certain amount of heat, the heat required to change 1 °C is the heat capacity of the temperature sensor, and the smaller the heat capacity, the better. The temperature sensor heat transfer needs to overcome the thermal resistance, which is directly related to the structure and size of the component. Metal is a good conductor of heat, and the size of the thermal resistance is often affected by the air gap of the temperature sensor, the insulation, and the protective sleeve.
Temperature sensors have large time constants and hysteresis, usually ranging from tens of seconds to minutes. Therefore, the influence on the measurement and control temperature is very large, especially the stability of the temperature control system. Therefore, in the field application, in addition to the temperature sensor with a small time constant and hysteresis, it should also pay attention to the installation method of the temperature sensor. That is to say, there must be a certain insertion depth when installing, especially the thermal resistance. If the insertion depth is not enough, it will cause a large error; When the process pipe is thinner, it is necessary to locally thicken the pipe, or try to install the temperature sensor on the elbow of the pipe, so that the temperature sensor is facing the flow direction of the fluid; When measuring the temperature of the gas-liquid medium, it is preferable to measure the liquidus temperature because the dynamic characteristics and stability of the liquidus temperature are superior to the gas phase temperature; If necessary, it is also possible to fill metal foil or other heat-conducting material between the protective tube and the thermal element (the armored thermocouple or armored platinum resistor is filled with high-purity alumina powder between the protective tube and the component). For the thermocouple, an open-ended or shell-type thermocouple can also be used.
PREVIOUS:NONE
NEXT:The development trend of sensor application technology in Car
NEXT:The development trend of sensor application technology in Car