Structural Selection of Temperature Sensors
With the advancement of electronic technology, information technology has gradually become the mainstream in people's lives. The three foundations of modern information technology are information collection (i.e. sensor technology), information transmission (communication technology) and information processing (computer technology). Sensors are cutting-edge products of information technology, especially temperature sensors (temperature sensor classification). So, what is a temperature sensor? Simply put, a temperature sensor refers to a sensor that uses the laws of various physical properties of matter to change with temperature to convert temperature into electricity (working principle of temperature sensor). It is the core part of the temperature measuring instrument (how to use the temperature sensor).
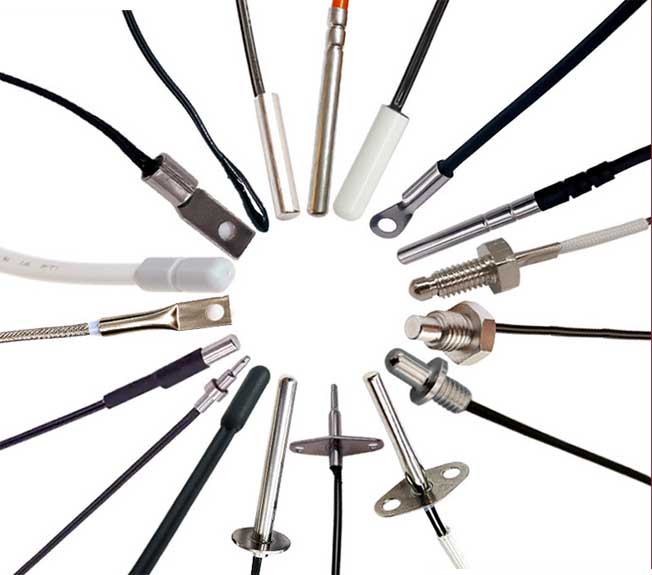
Development of temperature sensors
New temperature sensors in the world are developing from analog to digital, from integration to intelligence and networking. The development of temperature sensors has roughly gone through the following three stages:
(1) Traditional discrete temperature sensor (including sensitive element). The first smart temperature sensor launched in the mid-1990s used an 8-bit A/D converter, which had low temperature measurement accuracy and a resolution of only 1°C. Foreign countries have successively introduced a variety of high-precision, high-resolution intelligent temperature sensors, using 9~12-bit A/D converters, and the resolution can generally reach 0.5~0.0625°C.
(2) Simulation of integrated temperature sensor/controller. The DS1624 high-resolution intelligent temperature sensor newly developed by DALLAS Semiconductor Company in the United States can output 13-bit binary data, with a resolution of up to 0.03125°C and a temperature measurement accuracy of ±0.2°C. In order to improve the conversion rate of multi-channel intelligent temperature sensors, some chips also use high-speed successive approximation A/D converters. Taking the AD7817 5-channel intelligent temperature sensor as an example, its conversion time for the local sensor and each remote sensor is only 27us and 9us respectively.
(3) Intelligent temperature sensor. After entering the 21st century, intelligent temperature sensors are developing rapidly in high-tech directions such as high precision, multi-function, bus standardization, high reliability and security, development of virtual sensors and network sensors, and development of single-chip temperature measurement systems. At present, the bus technology of intelligent temperature sensors has also been standardized and normalized. The buses used mainly include single-wire (1-Wire) bus, I2C bus, SMBus bus and spI bus. As a slave, the temperature sensor can communicate with the host through a dedicated bus interface.
Let's take the MAX6625 intelligent digital temperature sensor as an example to introduce in detail what a temperature sensor is.
Intelligent digital temperature sensor MAX6625 structure
The MAX6625 smart digital temperature sensor mainly includes a bandgap reference voltage source and temperature sensor, A/D converter, 5 control registers (address pointer register, temperature data register, upper limit temperature register, lower limit temperature register and configuration register), set temperature Point comparator, fault queue counter and I2C serial bus interface circuit, etc. Its structural block diagram is shown in the figure.
Temperature sensor MAX6625 structure diagram
Intelligent digital temperature sensor MAX6625 pin function
MAX6625 adopts SOT23-6 miniaturized package. As shown in the figure.
Temperature sensor MAX6625 pinout
Its pin functions are as follows: SDA is a 12C compatible serial bidirectional data line. SCL is a 12C compatible serial clock line. ADD is: I2C compatible address setting terminal; 0T is the temperature alarm output terminal; Vs is the power supply; GND is the power ground.
Application of intelligent digital temperature sensor MAX6625
The MAX6625 can be used in fan control, temperature alarms, system temperature control and industrial equipment. Here are some application examples of distributed temperature monitoring and display. Only the connection circuit between the microcontroller and four MAX6625s is given. As shown below.
Connection between microcontroller and MAX6625
When applying programming, you should first set the MAX6625 with the microcontroller according to the system requirements, and then read the value of the temperature register in the MAX6625.
Setup program for intelligent digital temperature sensor MAX6625
In distributed multi-point temperature measurement or monitoring applications, the initial setup of the MAX6625 includes selecting the MAX6625, writing data to the configuration register, and writing to the high and low temperature registers. The following takes device 1 as an example for programming. Since AT89C51 does not have a dedicated 12C bus interface, the analog 12C interface is used for programming here.
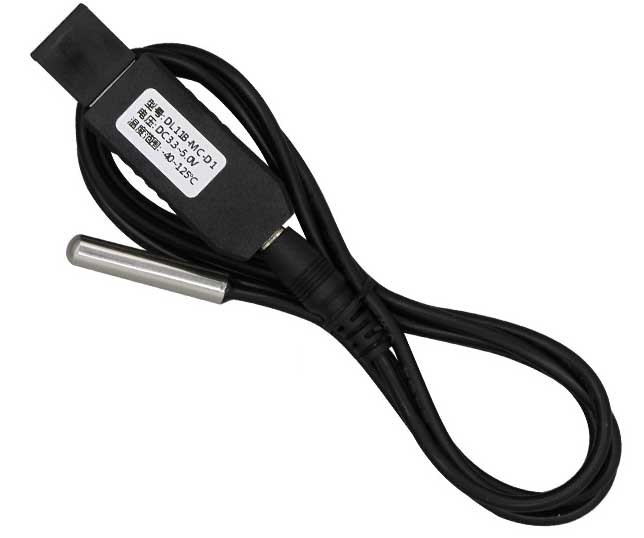
(1) Configuration register writing procedure
WRIte: LCALL START: Generate the start bit
MOV A.#10010000B;MAX6625 device 1
Address.R/W=O
LCALL WRBYT: Write device address
LCALL CACK: Query MAX6625 response
JB FO, WRITE; no response and restart
MOV A, #00000001B; There is a response
LcALL WRBYT: Write configuration register address
LCALL CACK
JB F0, WRITE
MOV A, #00010000B: Write configuration register data
LCALL WRBYT
LCALL CACK
JB FO, WRITE
LCALL STOP ; generate stop bit
RET
(2) Writing procedures for high and low temperature registers
WRWEl: LCALL STAlit; generate start bit
MOV A.#10010000B;MAX6625 device l
Write the address, R/W=O
LCALL WRBYT: Write device address
LCALL CACK: Query MAX6625 response
JB F0, WRITEl; no response and restart
MOV A.#00000011B; There is a response
LCALL WRBYT: Write high temperature register address
LCALL CACK
JB F0,WRITEl
MOV A, #01010000B; write high temperature register high
8 bits
LCALL WRBYT
ICAL CACK
JB FO, WRITEl
MOV A, #00OO000B: Write the lower 8 bits of the high temperature register
LCALL WRBYT
LCALL CACK
JB F0,WRITEl
LCALL STOP
RET
Programming of cryogenic registers only requires changing the address and data.
Summarize
Temperature sensors are widely used in fields such as industrial and agricultural production, scientific research, and daily life, and their number ranks first among all kinds of sensors. This article briefly introduces the development process of temperature sensors, taking the intelligent digital temperature sensor MAX6625 as an example. The structure, pin function, application and setting program writing of the temperature sensor are analyzed in detail.
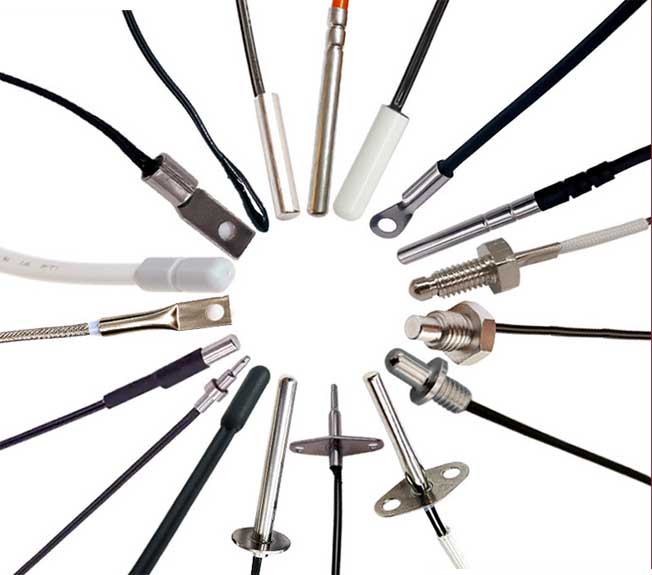
Development of temperature sensors
New temperature sensors in the world are developing from analog to digital, from integration to intelligence and networking. The development of temperature sensors has roughly gone through the following three stages:
(1) Traditional discrete temperature sensor (including sensitive element). The first smart temperature sensor launched in the mid-1990s used an 8-bit A/D converter, which had low temperature measurement accuracy and a resolution of only 1°C. Foreign countries have successively introduced a variety of high-precision, high-resolution intelligent temperature sensors, using 9~12-bit A/D converters, and the resolution can generally reach 0.5~0.0625°C.
(2) Simulation of integrated temperature sensor/controller. The DS1624 high-resolution intelligent temperature sensor newly developed by DALLAS Semiconductor Company in the United States can output 13-bit binary data, with a resolution of up to 0.03125°C and a temperature measurement accuracy of ±0.2°C. In order to improve the conversion rate of multi-channel intelligent temperature sensors, some chips also use high-speed successive approximation A/D converters. Taking the AD7817 5-channel intelligent temperature sensor as an example, its conversion time for the local sensor and each remote sensor is only 27us and 9us respectively.
(3) Intelligent temperature sensor. After entering the 21st century, intelligent temperature sensors are developing rapidly in high-tech directions such as high precision, multi-function, bus standardization, high reliability and security, development of virtual sensors and network sensors, and development of single-chip temperature measurement systems. At present, the bus technology of intelligent temperature sensors has also been standardized and normalized. The buses used mainly include single-wire (1-Wire) bus, I2C bus, SMBus bus and spI bus. As a slave, the temperature sensor can communicate with the host through a dedicated bus interface.
Let's take the MAX6625 intelligent digital temperature sensor as an example to introduce in detail what a temperature sensor is.
Intelligent digital temperature sensor MAX6625 structure
The MAX6625 smart digital temperature sensor mainly includes a bandgap reference voltage source and temperature sensor, A/D converter, 5 control registers (address pointer register, temperature data register, upper limit temperature register, lower limit temperature register and configuration register), set temperature Point comparator, fault queue counter and I2C serial bus interface circuit, etc. Its structural block diagram is shown in the figure.
Temperature sensor MAX6625 structure diagram
Intelligent digital temperature sensor MAX6625 pin function
MAX6625 adopts SOT23-6 miniaturized package. As shown in the figure.
Temperature sensor MAX6625 pinout
Its pin functions are as follows: SDA is a 12C compatible serial bidirectional data line. SCL is a 12C compatible serial clock line. ADD is: I2C compatible address setting terminal; 0T is the temperature alarm output terminal; Vs is the power supply; GND is the power ground.
Application of intelligent digital temperature sensor MAX6625
The MAX6625 can be used in fan control, temperature alarms, system temperature control and industrial equipment. Here are some application examples of distributed temperature monitoring and display. Only the connection circuit between the microcontroller and four MAX6625s is given. As shown below.
Connection between microcontroller and MAX6625
When applying programming, you should first set the MAX6625 with the microcontroller according to the system requirements, and then read the value of the temperature register in the MAX6625.
Setup program for intelligent digital temperature sensor MAX6625
In distributed multi-point temperature measurement or monitoring applications, the initial setup of the MAX6625 includes selecting the MAX6625, writing data to the configuration register, and writing to the high and low temperature registers. The following takes device 1 as an example for programming. Since AT89C51 does not have a dedicated 12C bus interface, the analog 12C interface is used for programming here.
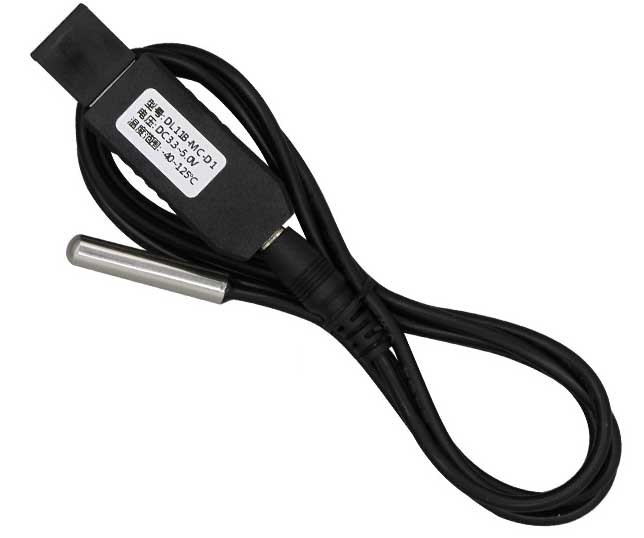
(1) Configuration register writing procedure
WRIte: LCALL START: Generate the start bit
MOV A.#10010000B;MAX6625 device 1
Address.R/W=O
LCALL WRBYT: Write device address
LCALL CACK: Query MAX6625 response
JB FO, WRITE; no response and restart
MOV A, #00000001B; There is a response
LcALL WRBYT: Write configuration register address
LCALL CACK
JB F0, WRITE
MOV A, #00010000B: Write configuration register data
LCALL WRBYT
LCALL CACK
JB FO, WRITE
LCALL STOP ; generate stop bit
RET
(2) Writing procedures for high and low temperature registers
WRWEl: LCALL STAlit; generate start bit
MOV A.#10010000B;MAX6625 device l
Write the address, R/W=O
LCALL WRBYT: Write device address
LCALL CACK: Query MAX6625 response
JB F0, WRITEl; no response and restart
MOV A.#00000011B; There is a response
LCALL WRBYT: Write high temperature register address
LCALL CACK
JB F0,WRITEl
MOV A, #01010000B; write high temperature register high
8 bits
LCALL WRBYT
ICAL CACK
JB FO, WRITEl
MOV A, #00OO000B: Write the lower 8 bits of the high temperature register
LCALL WRBYT
LCALL CACK
JB F0,WRITEl
LCALL STOP
RET
Programming of cryogenic registers only requires changing the address and data.
Summarize
Temperature sensors are widely used in fields such as industrial and agricultural production, scientific research, and daily life, and their number ranks first among all kinds of sensors. This article briefly introduces the development process of temperature sensors, taking the intelligent digital temperature sensor MAX6625 as an example. The structure, pin function, application and setting program writing of the temperature sensor are analyzed in detail.