NTC thermistor test method for automotive air conditioner
The thermistor is a resistor that differs in resistance depending on the temperature. It is widely used in automotive electronic controllers, especially automotive air conditioners, lithium battery management systems (BMS), and vehicle power controllers, all of which require modules for thermistors. The NTC thermistor is the resistance whose resistance value decreases as the temperature increases. Because of its temperature sensitivity, high precision, and low price, it is widely used in various temperature detection applications. However, the resistance value of the NTC thermistor has a nonlinear relationship with the temperature, so it is difficult to test in practical applications.
In the existing automotive air conditioners on the market, there are mainly two ways to obtain the temperature of the NTC thermistor applied thereto. One is to directly use the ideal B25 value as well as the RT value. Using this method makes it difficult to set the thermistor to an ideal value when it is actually produced. If the application is applied electronically according to the ideal value, the product will have a large error.
The other is to directly input the RT meter provided by the thermistor manufacturer into the car air conditioner controller. However, because the number of RT-tables provided by manufacturers is still very large, software engineers need to input one by one, which not only has a large workload, but also human error; Either the value in the RT table is very small, and the middle is directly processed linearly, resulting in a large error. Therefore, it is necessary to test the thermistor used in the car air conditioner before the car air conditioner is put into use to verify the validity of the RT meter data and ensure that the car air conditioner has high temperature control accuracy.
Today, we introduce a NTC thermistor test method for automotive air conditioners, which selects a third-order polynomial fitting formula based on the Steinhart-Hart equation. The RT table data values provided by the manufacturer of the NTC thermistor are fitted and analyzed, and the fitted data is compared with the original data. If the resulting residual exceeds a predetermined threshold, prompt to review the NTC thermistor. Moreover, for the NTC thermistor with less RT table data, the characteristic curve segmentation interpolation method is adopted. The RT table data is corrected and filtered by software to give a new set of RT table data suitable for the application, which provides a reference for the selection of NTC thermistors. Specific steps are as follows:
(1) Select the third-order polynomial fitting formula for curve fitting the RT table data of NTC thermistor, as follows:
RT=R25exp[A+B/T+C/T2+D/T3](1) or
Wherein, RT is a resistance value when the temperature is T, T is a Fahrenheit temperature, R25 is a resistance value when the room temperature is 25 ° C, and A, B, C, D, A1{C}{C}{C}{C}{C}{C}{C}{C}{C}, B1, C1, and D1 are constant;
(2) Convert the RT table data values provided by the NTC thermistor manufacturer into a constant matrix (Tincar<i>{C}{C}{C}{C}{C}{C}{C}{C}{C})j. Where i is the number of columns of the matrix, j is the number of rows of the matrix, and (Tincar<i>)j (abbreviated as Tincar<0>) is the temperature parameter in the RT table data;
(3) Using the software to analyze the characteristic curve of the constant matrix (Tincar<i>)j;
(4) Using the software to analyze the temperature parameters of the NTC thermistor to see if it meets the design requirements of the automotive air conditioner;
(5) Convert (Tincar<0>)j to Fahrenheit temperature Tmpm(0≤m≤j-1) (abbreviated as Tmp):
Tmp:=Tincar<0>+273.15(3)
(6) The data other than (Tincar<i>) in the constant matrix Tincar<0> and the calculated Tmpm value are brought into the polynomial fitting formula (2), and the constants A1, B1, C1, and D1 are calculated. And get a constant matrix
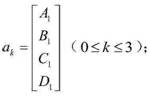
(7) Bring Tmp and akinto the following equation (4) to calculate the resistance value RT(Tmp·K,ash) of the fitted NTC thermistor;
(8) Using the software, the fitted resistance value RT(Tmp·K,ash){C}{C}{C}is compared with the RT table data value provided by the NTC thermistor manufacturer and the residual analysis is performed. When the obtained residual exceeds a preset threshold, prompting to review the thermistor;
(9) Correct the RT table data by curve segmentation interpolation, and A/D sampling after software filtering to obtain a new set of RT table data suitable for application, which provides reference for selecting NTC thermistor. And in a given set of new RT-table data suitable for the application, the thermistor is given as the emergency temperature data of the wire harness disconnection condition of the temperature sensor.
As an improvement, in the process of performing curve segmentation interpolation on the RT table data, an equal-step data interpolation with a step size of 1 is performed for the resistance value in the temperature range of -10 to 40 ° C in the RT table data. An equal-step data interpolation of a step size of 5 is performed for the resistance value of the remaining temperature interval.
The filtering formula used for software filtering is:

rem=[rem+filt*(2^f_rate-1)+input]&(2^f_rate-1)
Among them, filt is the loop filter value of the software filter, input is the input current value of the software filter, and f_rate is the filter speed of the software filter.
Compared with the traditional method of calculating using the exponential formula, the test method can be more consistent with the measured data in a larger temperature range; Moreover, the formula used is relatively simple, the calculation amount of the fitting parameters and the calculation amount of the equation are less, so the calculation speed is faster; The test method has higher precision, consumes less computer storage space, and is faster in engineering applications; This test method can also be used to evaluate the validity of the RT meter data provided by the NTC thermistor manufacturer, and whether its accuracy meets the design requirements, and has a certain guiding role in the purchase management of the thermistor. It avoids the error caused by directly designing the ideal B25 value or RT value, and also improves the error caused by the thermistor to the actual product.
In the existing automotive air conditioners on the market, there are mainly two ways to obtain the temperature of the NTC thermistor applied thereto. One is to directly use the ideal B25 value as well as the RT value. Using this method makes it difficult to set the thermistor to an ideal value when it is actually produced. If the application is applied electronically according to the ideal value, the product will have a large error.
The other is to directly input the RT meter provided by the thermistor manufacturer into the car air conditioner controller. However, because the number of RT-tables provided by manufacturers is still very large, software engineers need to input one by one, which not only has a large workload, but also human error; Either the value in the RT table is very small, and the middle is directly processed linearly, resulting in a large error. Therefore, it is necessary to test the thermistor used in the car air conditioner before the car air conditioner is put into use to verify the validity of the RT meter data and ensure that the car air conditioner has high temperature control accuracy.
Today, we introduce a NTC thermistor test method for automotive air conditioners, which selects a third-order polynomial fitting formula based on the Steinhart-Hart equation. The RT table data values provided by the manufacturer of the NTC thermistor are fitted and analyzed, and the fitted data is compared with the original data. If the resulting residual exceeds a predetermined threshold, prompt to review the NTC thermistor. Moreover, for the NTC thermistor with less RT table data, the characteristic curve segmentation interpolation method is adopted. The RT table data is corrected and filtered by software to give a new set of RT table data suitable for the application, which provides a reference for the selection of NTC thermistors. Specific steps are as follows:
(1) Select the third-order polynomial fitting formula for curve fitting the RT table data of NTC thermistor, as follows:
RT=R25exp[A+B/T+C/T2+D/T3](1) or

Wherein, RT is a resistance value when the temperature is T, T is a Fahrenheit temperature, R25 is a resistance value when the room temperature is 25 ° C, and A, B, C, D, A1{C}{C}{C}{C}{C}{C}{C}{C}{C}, B1, C1, and D1 are constant;
(2) Convert the RT table data values provided by the NTC thermistor manufacturer into a constant matrix (Tincar<i>{C}{C}{C}{C}{C}{C}{C}{C}{C})j. Where i is the number of columns of the matrix, j is the number of rows of the matrix, and (Tincar<i>)j (abbreviated as Tincar<0>) is the temperature parameter in the RT table data;
(3) Using the software to analyze the characteristic curve of the constant matrix (Tincar<i>)j;
(4) Using the software to analyze the temperature parameters of the NTC thermistor to see if it meets the design requirements of the automotive air conditioner;
(5) Convert (Tincar<0>)j to Fahrenheit temperature Tmpm(0≤m≤j-1) (abbreviated as Tmp):
Tmp:=Tincar<0>+273.15(3)
(6) The data other than (Tincar<i>) in the constant matrix Tincar<0> and the calculated Tmpm value are brought into the polynomial fitting formula (2), and the constants A1, B1, C1, and D1 are calculated. And get a constant matrix
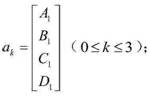
(7) Bring Tmp and akinto the following equation (4) to calculate the resistance value RT(Tmp·K,ash) of the fitted NTC thermistor;
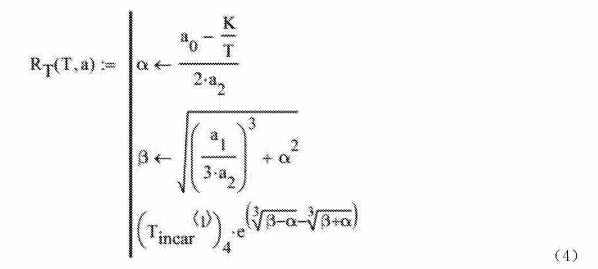
(9) Correct the RT table data by curve segmentation interpolation, and A/D sampling after software filtering to obtain a new set of RT table data suitable for application, which provides reference for selecting NTC thermistor. And in a given set of new RT-table data suitable for the application, the thermistor is given as the emergency temperature data of the wire harness disconnection condition of the temperature sensor.
As an improvement, in the process of performing curve segmentation interpolation on the RT table data, an equal-step data interpolation with a step size of 1 is performed for the resistance value in the temperature range of -10 to 40 ° C in the RT table data. An equal-step data interpolation of a step size of 5 is performed for the resistance value of the remaining temperature interval.
The filtering formula used for software filtering is:

rem=[rem+filt*(2^f_rate-1)+input]&(2^f_rate-1)
Among them, filt is the loop filter value of the software filter, input is the input current value of the software filter, and f_rate is the filter speed of the software filter.
Compared with the traditional method of calculating using the exponential formula, the test method can be more consistent with the measured data in a larger temperature range; Moreover, the formula used is relatively simple, the calculation amount of the fitting parameters and the calculation amount of the equation are less, so the calculation speed is faster; The test method has higher precision, consumes less computer storage space, and is faster in engineering applications; This test method can also be used to evaluate the validity of the RT meter data provided by the NTC thermistor manufacturer, and whether its accuracy meets the design requirements, and has a certain guiding role in the purchase management of the thermistor. It avoids the error caused by directly designing the ideal B25 value or RT value, and also improves the error caused by the thermistor to the actual product.