Medical High Precision NTC Thermistor Manufacturer
Medical high-precision NTC thermistor can be widely used in the medical industry for temperature measurement and temperature control. It has excellent consistency, repeatability and stability, and the measurement range can be in the range of 0 to +70 °C. The measurement accuracy of each point can be controlled within ±0.2 °C to ensure the accuracy of each temperature measurement point. At the same time, in addition to its small size, fast response and long service life, this thermistor has the characteristics of high resistance and large slope of temperature characteristic curve. Using medical high-precision NTC thermistor, it can more accurately and effectively achieve the effect of temperature measurement and temperature control. Make electronic equipment more stable and more accurate temperature measurement to reduce test errors.
NTC manufacturers have made new progress in the variety and production scale of NTC thermistors. The isostatic pressing technology and thick film process technology of medical NTC thermistors have been improved and promoted in the production and application of NTC components. NTC thermistors vary from 10Ω to 1000000Ω at room temperature and have a temperature coefficient of -2% to -6.5%. However, in the existing production methods, the temperature control accuracy generally reaches 0.3 ° C ~ 1.5 ° C, although some products temperature control accuracy can be controlled within 0.2 ° C, but only limited to a single point or a narrow temperature range. In order to overcome the shortcomings of the prior art, today we introduce a method for producing a medical high-precision NTC thermistor with high precision, wide measurement range, and multi-point measurement accuracy of ±0.2 °C.
The production method of the medical high-precision NTC thermistor comprises the following steps:
1) Powder preparation: According to the target B value, the powder is prepared in proportion, and the main components of the powder are CoO, NiO, MnO, CuO, ZnO, MgO, FeO, CrO, ZrO, TiO, etc.;
2) ball milling: The prepared powder is charged into a rolling tank and zirconium balls are added, and a certain proportion of solvent is added in two portions. Solvents mainly include: Ethanol, toluene, dispersant, CK24, plasticizer. The main purpose of ball milling is to mix the powder evenly and grind it into nano-powder;
3) Thin belt pressure forming: The ball-milled slurry is formed into a thin strip by a casting method, and the thickness of the thin strip is 70 μm±2 μm; the formed thin strip is stripped, laminated, sliced, and finally pressed into a green ceramic with hot water;
4) Raw embryo sintering: The pressed green ceramics are slowly raised to 1120~1350 °C at a rate of 1 °C/min in a high-temperature sintering furnace, and kept for 2~3 hours; then slowly cooled down to 100 °C at a rate of 1 °C/min, and then naturally cooled; a semiconductor material having a spinel structure, that is, an NTC ceramic sheet;
5) The tiles are silver: The prepared silver paste is printed on the two ends of the NTC ceramic plate by the silver printing device, and the electrode layer is formed on both ends of the NTC ceramic piece; that is, the NTC silver piece is obtained;
6) Burning silver: The silver plated NTC silver sheet is sintered through a silver burning furnace to sufficiently bond the silver layer and the ceramic sheet to form a fixed structure;
7) dicing: According to the target resistance value, the silver-plated NTC silver sheet is precisely diced by a dicing machine to obtain a rectangular parallelepiped or a square-shaped NTC chip;
The measurement range can be controlled within ±0.2°C per point in the range of 0~70°C, ensuring the accuracy of each temperature measurement point;
8) Welding: The wire and the NTC chip are soldered into a two-wire resistor or a three-wire resistor according to product characteristics;
9) Encapsulation: Both the two-wire resistor and the three-wire resistor can be encapsulated with an environmentally friendly adhesive;
10) Curing: The encapsulant is fixed by curing in a high temperature oven;
11) Test sorting: Sorted by the thermistor tester, the medical high-precision NTC thermistor is finally obtained.
NTC manufacturers have made new progress in the variety and production scale of NTC thermistors. The isostatic pressing technology and thick film process technology of medical NTC thermistors have been improved and promoted in the production and application of NTC components. NTC thermistors vary from 10Ω to 1000000Ω at room temperature and have a temperature coefficient of -2% to -6.5%. However, in the existing production methods, the temperature control accuracy generally reaches 0.3 ° C ~ 1.5 ° C, although some products temperature control accuracy can be controlled within 0.2 ° C, but only limited to a single point or a narrow temperature range. In order to overcome the shortcomings of the prior art, today we introduce a method for producing a medical high-precision NTC thermistor with high precision, wide measurement range, and multi-point measurement accuracy of ±0.2 °C.
The production method of the medical high-precision NTC thermistor comprises the following steps:
1) Powder preparation: According to the target B value, the powder is prepared in proportion, and the main components of the powder are CoO, NiO, MnO, CuO, ZnO, MgO, FeO, CrO, ZrO, TiO, etc.;
2) ball milling: The prepared powder is charged into a rolling tank and zirconium balls are added, and a certain proportion of solvent is added in two portions. Solvents mainly include: Ethanol, toluene, dispersant, CK24, plasticizer. The main purpose of ball milling is to mix the powder evenly and grind it into nano-powder;
3) Thin belt pressure forming: The ball-milled slurry is formed into a thin strip by a casting method, and the thickness of the thin strip is 70 μm±2 μm; the formed thin strip is stripped, laminated, sliced, and finally pressed into a green ceramic with hot water;
4) Raw embryo sintering: The pressed green ceramics are slowly raised to 1120~1350 °C at a rate of 1 °C/min in a high-temperature sintering furnace, and kept for 2~3 hours; then slowly cooled down to 100 °C at a rate of 1 °C/min, and then naturally cooled; a semiconductor material having a spinel structure, that is, an NTC ceramic sheet;
5) The tiles are silver: The prepared silver paste is printed on the two ends of the NTC ceramic plate by the silver printing device, and the electrode layer is formed on both ends of the NTC ceramic piece; that is, the NTC silver piece is obtained;
6) Burning silver: The silver plated NTC silver sheet is sintered through a silver burning furnace to sufficiently bond the silver layer and the ceramic sheet to form a fixed structure;
7) dicing: According to the target resistance value, the silver-plated NTC silver sheet is precisely diced by a dicing machine to obtain a rectangular parallelepiped or a square-shaped NTC chip;
The measurement range can be controlled within ±0.2°C per point in the range of 0~70°C, ensuring the accuracy of each temperature measurement point;
8) Welding: The wire and the NTC chip are soldered into a two-wire resistor or a three-wire resistor according to product characteristics;
9) Encapsulation: Both the two-wire resistor and the three-wire resistor can be encapsulated with an environmentally friendly adhesive;
10) Curing: The encapsulant is fixed by curing in a high temperature oven;
11) Test sorting: Sorted by the thermistor tester, the medical high-precision NTC thermistor is finally obtained.
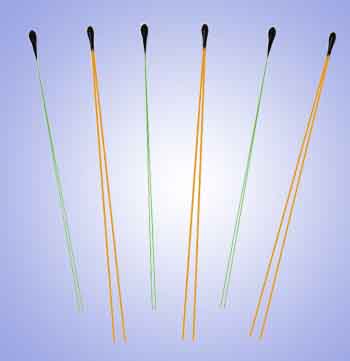