Analysis of Principle and Application of Ceramic Capacitive Pressure Sensor
- PRODUCT DETAIL
What is a ceramic capacitive pressure sensor?
Ceramic capacitors, as a main technical route in pressure sensors, have the advantages of corrosion resistance, impact resistance, and good dielectric compatibility. Pressure sensors are a large category of sensors and are widely used in automotive, industrial, and Internet of Things fields.
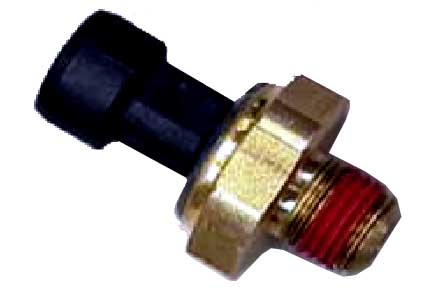
Common pressure sensor technology types
Pressure sensors are generally used to measure the pressure of the gas or liquid atmosphere in which the sensor's sensitive components are located, and are generally used to feed back to the system's main control unit to achieve accurate system control.
As a large category of sensors, pressure sensors are widely used in different industries such as automotive, industrial, home appliances, and consumer electronics. Commonly used pressure sensors are distinguished from the sensing principle, which mainly includes the following categories:
-Silicon piezoresistive technology
-Ceramic Resistor Technology
-Glass microfusing technology
-Ceramic Capacitor Technology
Silicon piezoresistive technology is realized by the piezoresistive characteristics of semiconductors. The piezoresistive properties of semiconductor materials depend on factors such as the type of material, the doping concentration, and the crystal orientation of the crystal. This technology can be implemented using semiconductor technology, and has the advantages of small size, high yield, low cost, and high signal output sensitivity. The shortcomings are mainly reflected in the low tolerance of the medium, poor temperature characteristics and poor long-term stability. It is common in the low and medium pressure range, such as 5kPa ~ 700kPa. The industry also has solutions to improve the dielectric resistance of silicon piezoresistive technology through special packaging processes. Such as oil filling, back pressure and other technologies, but it also brings problems such as a substantial increase in costs.
Ceramic resistor technology uses a thick film printing process to print a Wheatstone bridge on the surface of a ceramic structure, and uses the varistor effect to convert the pressure signal of the medium into a voltage signal. Ceramic resistor technology has the advantages of moderate cost and simple process. At present, many domestic manufacturers provide ceramic resistance pressure sensor cores. However, the signal output sensitivity of this technology is low, the range is generally limited to 500kPa ~ 10MPa, and the conventional hollow structure only bears the pressure of the diaphragm, which has poor resistance to overload. When the pressure of the medium to be measured is overloaded, the ceramic resistance sensor will risk the diaphragm rupture and the medium leak.
Glass microfusing technology uses a high-temperature sintering process that combines a silicon strain gauge with a stainless steel structure. A silicon strain gage equivalent of four resistors makes up a Wheatstone bridge. When there is a medium pressure on the other side of the stainless steel diaphragm, the stainless steel diaphragm generates a slight deformation that causes the bridge to change, forming a voltage signal proportional to the pressure change. The glass micro-melting process is difficult to realize and the cost is high. The main advantage is that the medium has good tolerance and strong overload resistance. It is generally suitable for high pressure and ultra high pressure ranges, such as 10MPa ~ 200MPa, and its application is limited.
Ceramic capacitor technology uses a fixed ceramic base and a movable ceramic diaphragm structure. The movable diaphragm is sealed and fixed with the base through a method such as glass slurry.
An electrode pattern is printed on the inside between the two to form a variable capacitor. When the medium pressure on the diaphragm changes, the capacitance between the two changes accordingly. The signal is converted and conditioned by a conditioning chip and then output to a subsequent stage for use.
Ceramic capacitor technology has the advantages of moderate cost, wide measuring range, good temperature characteristics, consistency, and long-term stability. From the international point of view, it is widely used in automotive and industrial process control and other fields, represented by American Sensata and Swiss E + H. Since the capacitance signal is different from the resistance signal, the signal processing circuit is required to be higher. The sensor design needs to consider the capacitance and signal conditioning chip ASIC together. At present, only Yaxun Electronics is able to provide a complete solution for the integration of both.
Product design of ceramic capacitive pressure sensor
Ceramic Capacitive Pressure Sensor Core Pressure Measurement Principle
Ceramic capacitors, as a main technical route in pressure sensors, have the advantages of corrosion resistance, impact resistance, and good dielectric compatibility. Pressure sensors are a large category of sensors and are widely used in automotive, industrial, and Internet of Things fields.
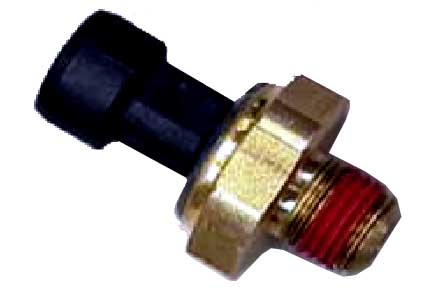
Common pressure sensor technology types
Pressure sensors are generally used to measure the pressure of the gas or liquid atmosphere in which the sensor's sensitive components are located, and are generally used to feed back to the system's main control unit to achieve accurate system control.
As a large category of sensors, pressure sensors are widely used in different industries such as automotive, industrial, home appliances, and consumer electronics. Commonly used pressure sensors are distinguished from the sensing principle, which mainly includes the following categories:
-Silicon piezoresistive technology
-Ceramic Resistor Technology
-Glass microfusing technology
-Ceramic Capacitor Technology
Silicon piezoresistive technology is realized by the piezoresistive characteristics of semiconductors. The piezoresistive properties of semiconductor materials depend on factors such as the type of material, the doping concentration, and the crystal orientation of the crystal. This technology can be implemented using semiconductor technology, and has the advantages of small size, high yield, low cost, and high signal output sensitivity. The shortcomings are mainly reflected in the low tolerance of the medium, poor temperature characteristics and poor long-term stability. It is common in the low and medium pressure range, such as 5kPa ~ 700kPa. The industry also has solutions to improve the dielectric resistance of silicon piezoresistive technology through special packaging processes. Such as oil filling, back pressure and other technologies, but it also brings problems such as a substantial increase in costs.
Ceramic resistor technology uses a thick film printing process to print a Wheatstone bridge on the surface of a ceramic structure, and uses the varistor effect to convert the pressure signal of the medium into a voltage signal. Ceramic resistor technology has the advantages of moderate cost and simple process. At present, many domestic manufacturers provide ceramic resistance pressure sensor cores. However, the signal output sensitivity of this technology is low, the range is generally limited to 500kPa ~ 10MPa, and the conventional hollow structure only bears the pressure of the diaphragm, which has poor resistance to overload. When the pressure of the medium to be measured is overloaded, the ceramic resistance sensor will risk the diaphragm rupture and the medium leak.
Glass microfusing technology uses a high-temperature sintering process that combines a silicon strain gauge with a stainless steel structure. A silicon strain gage equivalent of four resistors makes up a Wheatstone bridge. When there is a medium pressure on the other side of the stainless steel diaphragm, the stainless steel diaphragm generates a slight deformation that causes the bridge to change, forming a voltage signal proportional to the pressure change. The glass micro-melting process is difficult to realize and the cost is high. The main advantage is that the medium has good tolerance and strong overload resistance. It is generally suitable for high pressure and ultra high pressure ranges, such as 10MPa ~ 200MPa, and its application is limited.
Ceramic capacitor technology uses a fixed ceramic base and a movable ceramic diaphragm structure. The movable diaphragm is sealed and fixed with the base through a method such as glass slurry.
An electrode pattern is printed on the inside between the two to form a variable capacitor. When the medium pressure on the diaphragm changes, the capacitance between the two changes accordingly. The signal is converted and conditioned by a conditioning chip and then output to a subsequent stage for use.
Ceramic capacitor technology has the advantages of moderate cost, wide measuring range, good temperature characteristics, consistency, and long-term stability. From the international point of view, it is widely used in automotive and industrial process control and other fields, represented by American Sensata and Swiss E + H. Since the capacitance signal is different from the resistance signal, the signal processing circuit is required to be higher. The sensor design needs to consider the capacitance and signal conditioning chip ASIC together. At present, only Yaxun Electronics is able to provide a complete solution for the integration of both.
Product design of ceramic capacitive pressure sensor
Ceramic Capacitive Pressure Sensor Core Pressure Measurement Principle
The core of a typical ceramic capacitive pressure sensor is a sealed gauge pressure structure, which is composed of a ceramic base, a deformable diaphragm, and a hollow sealed cavity. The pressure bearing surface is a deformable diaphragm. When the core bearing pressure changes, the deformed film will bend after bearing pressure, which will cause the substrate spacing to change and the capacitance between the plates to change. The capacitance change is converted into standard output (such as 0 ~ 5V voltage output, 4 ~ 20mA current output, I2C, SPI digital output, etc.) through the conditioning chip.
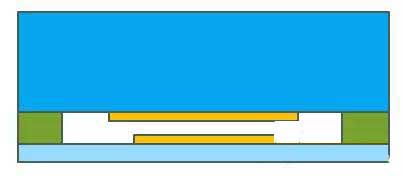
Figure 1: Sectional view of a ceramic capacitor pressure sensor under pressure
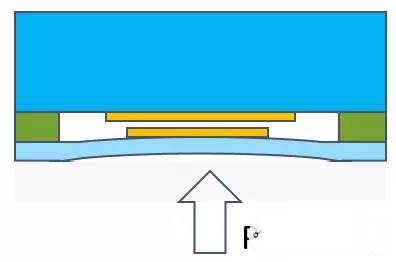
Figure 2: Cross-section view of a ceramic capacitor pressure sensor under pressure
Sealing structure of typical ceramic capacitor pressure sensor
In order to ensure air-tightness, in the design of ceramic capacitor pressure sensors, O-rings or gaskets are selected as the key components of the seal, of which O-rings are more common. Because O-rings have excellent linear sealing characteristics, the pressure range is wider than gaskets (gaskets are generally recommended for sealing within 2MPa) and other advantages.
The selection of parameters such as the size, material and hardness of the O-ring will directly affect the product performance of the final pressure sensor. It needs to be selected after considering the dimensions of the assembly, the type of medium to be measured, the operating temperature range and other factors.
Common O-ring materials in pressure sensors are: EPDM,
Hydrogenated nitrile rubber (HNBR),
Silicone rubber (QM),
Neoprene (CR), fluorine rubber (FKM), fluorosilicone rubber (MFQ), etc.
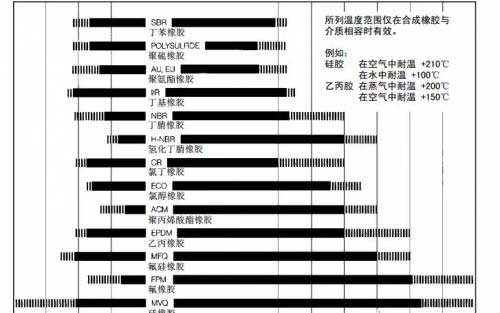
Figure 3: Operating temperature range of a typical O-ring material (source: Parker)
Generally speaking, automotive air-conditioning pressure sensors use HNBR or CR material O-rings, and oil pressure sensors use fluoro rubber. Automotive air brake pressure sensors can use O-rings made of silicone rubber; Even for the same kind of material, each manufacturer can extend its operating temperature range through special doping or polymerization treatment. There may be multiple optional materials to match for the same sensor application. In specific use, after consulting and confirming with the O-ring manufacturer, select the appropriate O-ring material and grade to design the sensor structure.
The general sealing structure of the ceramic capacitor pressure sensor is shown in the following figure:
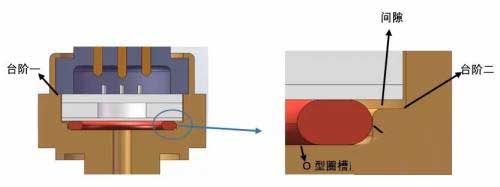
Figure 4: Schematic diagram of a typical ceramic capacitor sealing structure
After the pressure sensor is assembled, the bottom of the ceramic capacitor needs to maintain a certain distance from the metal case (the gap in the figure above). Generally, ceramic capacitor pressure sensors withstand positive pressure, so only the outer ring of the O-ring groove is retained to reduce the processing difficulty.
By controlling the height difference between the first step and the bottom of the O-ring groove in the figure above, the amount of compression of the O-ring is controlled.
The second step and the bottom of the O-ring groove form an O-ring groove, which defines the assembly position of the O-ring. In addition, the top of the O-ring groove needs to be rounded to prevent the O-ring from being cut by the housing after pressure is applied, and the bottom of the O-ring groove is rounded to reduce assembly stress.
Typical applications of ceramic capacitive pressure sensors
Ceramic capacitor pressure sensors can be widely used in pressure detection of water, gas and liquid due to their advantages such as corrosion resistance, impact resistance, no hysteresis, and strong medium compatibility. Particularly suitable for working in the harsh environment of automotive systems. For the emerging application market of pressure sensors such as the Internet of Things and home appliances, the impact resistance of ceramic capacitors can be applied to the water pressure measurement of water supply pipeline networks, which perfectly respond to the water hammer effect; For variable pressure pressure cooker applications, ceramic capacitor flat membrane structure can avoid clogging.
Typical applications of ceramic capacitor pressure sensors in the automotive field are shown in the following table:
Table 1: Typical applications of ceramic capacitive pressure sensors in the automotive field
Typical applications of ceramic capacitive pressure sensors in the Internet of Things and home appliances are shown in the following table:
Table 2: Typical applications of ceramic capacitive pressure sensors in the automotive field
Yaxun Electronics can provide ceramic capacitor pressure sensors with a working pressure range of 0.5MPa ~ 10MPa, multiple ranges are available, and waterproof versions are available
Combined with the special chip NSC9260 for capacitive signal conditioning, we can provide customers with complete capacitive sensor solutions. We can also provide customized sensor system solutions according to the actual needs of customers.