Abandoning NTC Electric Thermal Regulator - Using Analog Temperature Sensor
NTC electrothermal regulator and analog temperature sensor are two commonly used temperature detection solutions for most electronic applications. Deciding which technology is best for your application is a difficult task. .0However, I will tell you why some of the NTC electrothermal regulator should be discarded and the analog temperature sensor is used.
Figure 1 shows the comparison of output voltage and temperature. Note that the NTC thermistor requires a resistor network to help linearize its output. This is because their resistance vs temperature characteristics vary exponentially. Unlike NTC thermistors, analog temperature sensors do not require any additional components because they have a virtual linear output voltage. For example, in the full operating temperature range of the device from -50 ° C to 150 ° C, Texas Instruments' LMT87 analog temperature sensor provides a virtual linear output voltage for the entire device.
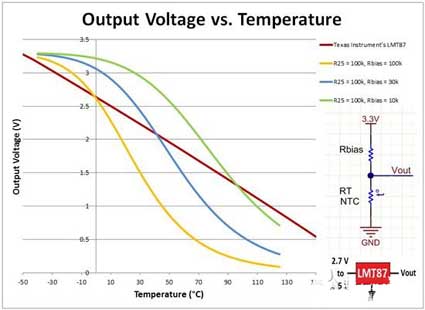
Figure 1 Relationship between output voltage (V) and temperature (°C)
Figure 2 shows the relationship between supply current and temperature. The LMT87 is typically 5.4μA with a maximum of 9μA. NTC Electrothermal Regulator networks tend to consume more power because their supply currents are much stronger and vary with temperature. Note that if you increase the resistance of the bias resistor, the supply current of the NTC Electrothermal Regulator network is reduced. But remember to also choose a bias resistor to ensure that the output voltage vs. temperature profile is linear over the expected temperature range. This compromise and balance is not required when using analog temperature sensors because they have a very constant low supply current and a virtual linear output voltage. Another disadvantage of NTC Electrothermal Regulator is that engineers must consider the self-heating effect because it causes other errors.
By abandoning the NTC Electrothermal Regulator and switching to TI's easy-to-use analog temperature sensor, you can avoid many NTC Electrothermal Regulator design issues.
Figure 1 shows the comparison of output voltage and temperature. Note that the NTC thermistor requires a resistor network to help linearize its output. This is because their resistance vs temperature characteristics vary exponentially. Unlike NTC thermistors, analog temperature sensors do not require any additional components because they have a virtual linear output voltage. For example, in the full operating temperature range of the device from -50 ° C to 150 ° C, Texas Instruments' LMT87 analog temperature sensor provides a virtual linear output voltage for the entire device.
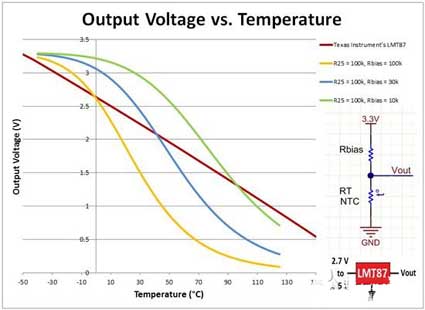
Figure 1 Relationship between output voltage (V) and temperature (°C)
Figure 2 shows the relationship between supply current and temperature. The LMT87 is typically 5.4μA with a maximum of 9μA. NTC Electrothermal Regulator networks tend to consume more power because their supply currents are much stronger and vary with temperature. Note that if you increase the resistance of the bias resistor, the supply current of the NTC Electrothermal Regulator network is reduced. But remember to also choose a bias resistor to ensure that the output voltage vs. temperature profile is linear over the expected temperature range. This compromise and balance is not required when using analog temperature sensors because they have a very constant low supply current and a virtual linear output voltage. Another disadvantage of NTC Electrothermal Regulator is that engineers must consider the self-heating effect because it causes other errors.
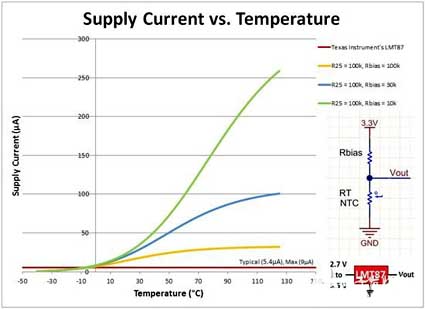
Figure 2 Relationship between supply current (μA) and temperature (°C)
By abandoning the NTC Electrothermal Regulator and switching to TI's easy-to-use analog temperature sensor, you can avoid many NTC Electrothermal Regulator design issues.